Table of Contents
- 1 What is Inventory?
- 2 Concept of Inventory Management
-
3 Purpose of Inventory
- 3.1 To Maintain Independence of Operations
- 3.2 To Meet Variations in Product Demand
- 3.3 Meet Customer Demand
- 3.4 To Allow Flexibility in Production Scheduling
- 3.5 Smooth Production and Operations
- 3.6 Buffer Against Supply Chain Uncertainties
- 3.7 Take Advantage of Economies of Scale
- 3.8 Support Seasonal or Cyclical Demand
- 3.9 Enable Quick Order Fulfillment
- 3.10 Flexibility in Pricing and Promotions
- 3.11 Hedge Against Price Volatility
- 3.12 Supply Chain Optimization
- 3.13 Strategic Value
- 3.14 To Take Advantage of Economic Purchase Order Size
- 3.15 Many Other Domain-specific C Reasons
- 4 Inventory Cost
- 5 FAQs About the What is Inventory?
What is Inventory?
Inventory is the stock of any item or resource used in an organization. An inventory system is a set of policies and controls that monitor levels of inventory and determine what levels Should be maintained, when stock should be replenished, and how large orders should be.
By convention, manufacturing inventory generally refers to items that contribute to or become part of a firm’s product output. Manufacturing inventory is typically classified into raw materials, finished products, component parts, supplies, and work-in-process.
In distribution, inventory is classified as in-transit, meaning that it is being moved in the system, and warehouse, which is inventory in a warehouse or distribution center. Retail sites carry inventory for immediate sale to customers. In services, inventory generally refers to the tangible goods to be sold and the supplies necessary to administer the service.
Concept of Inventory Management
Before we ask ourselves “What is inventory management” we need to, first of all, understand the definition of inventory. Inventory quite simply consists of materials and supplies in various formats held in stock by businesses to provide a service to their customers. Inventory can be sub-divided into a number of categories, three primary ones being:
-
Raw Material: Material that has not yet been processed in any format.
-
Work in Progress (WIP): Raw Material and other components which have been partially assembled or completed.
- Finished Product: Completed items ready for sale to Customers.
Effective inventory management is critical to delivering superior business results to most organizations whether in manufacturing or distribution. the key measurement for success in inventory management is having what you need, when you need it, and at the required location.
Different industries will have different perspectives in relation to what is inventory management but in general the concepts are mainly similar.
Most business organizations strive on a daily basis to improve their customer service performance and reducing lead times from order to delivery is a key performance improvement measure (KPI) The challenge however in achieving this improvement is to simultaneously reduce both inventory levels and freight costs whilst also minimizing out of stocks on critical items.
There are many activities you can focus on as part of an effective inventory management policy:
- Manage & Understand Your Customer Demand
- Increase Your Inventory Turnover
- Implement an Inventory Control Process
- Consider a “Kanban” System of Inventory Control
- Manage and Re-Organise Pour Warehouse
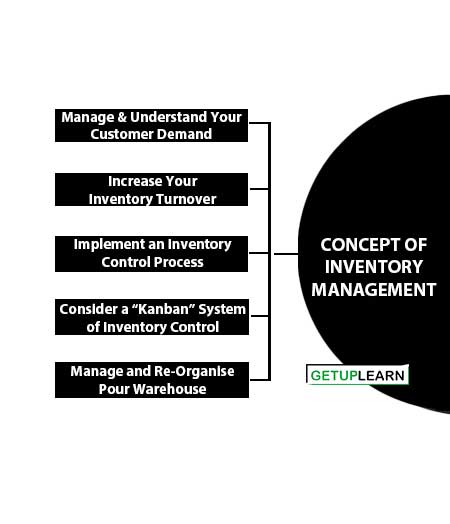
Manage & Understand Your Customer Demand
If this is inaccurate then you will end up with either over or under-supply. Both scenarios bring their own respective challenge.
Increase Your Inventory Turnover
As Inventory is capital-tied up including the charges for handling, storage, and management you will need to keep it to a minimum. A measure of progress is the number of times your stock turns usually on an annual basis. The calculation normally is made as follows, “ cost of goods sold divided by the average inventory for the period.
Implement an Inventory Control Process
Introduce an inventory cycle count system to quickly identify stock errors. The number of items counted should be statistically reflective of the number of transactions and appropriate measures implemented to resolve identified errors.
Consider a “Kanban” System of Inventory Control
It can be simply a series of colored cards which appear as the container of goods empties prompting the replenishment of more before a shortage develops.
Manage and Re-Organise Pour Warehouse
The principle of “a place for everything and everything in its place” should apply to storage areas as much as to manufacturing and other areas of business. Ensure your warehouse is well organized with clear signage in place. Segregation and a clear material flow should be obvious even to personnel not familiar with the area.
Implement Standard Operating Procedures: Formalise your operating activities with written inventory control procedures. These should be brief but specific with the test being a reader not familiar with the area or processes should on reviewing an SOP have a good understanding of the task being performed.
The best procedures are often those drafted by personnel actually carrying out the activity who also can be the best people in training peers and colleagues. Whether you operate within a large multi-store environment or a small business inventory management depends on understanding all the activities which can impact either negatively or positively on the performance.
In the process of understanding what is inventory management, there are numerous other activities to focus on and implement as part of an effective inventory program eg just in time inventory policies, and others.
Purpose of Inventory
The purpose of inventory in a business can be summarized as follows:
- To Maintain Independence of Operations
- To Meet Variations in Product Demand
- Meet Customer Demand
- To Allow Flexibility in Production Scheduling
- Smooth Production and Operations
- Buffer Against Supply Chain Uncertainties
- Take Advantage of Economies of Scale
- Support Seasonal or Cyclical Demand
- Enable Quick Order Fulfillment
- Flexibility in Pricing and Promotions
- Hedge Against Price Volatility
- Supply Chain Optimization
- Strategic Value
- To Take Advantage of Economic Purchase Order Size
- Many Other Domain-specific C Reasons
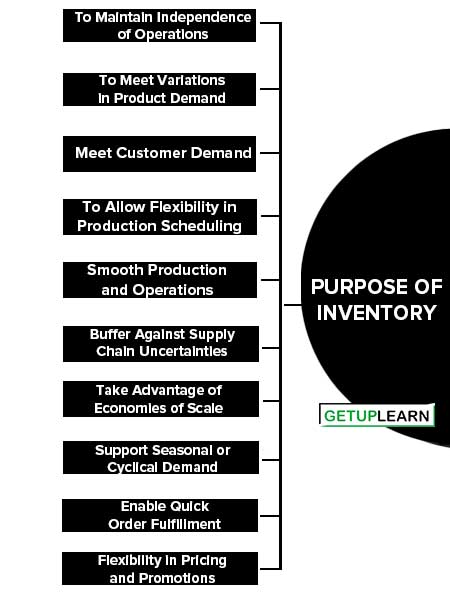
To Maintain Independence of Operations
A supply of materials at a work center allows that center flexibility in operations. For example, because there are costs for making each new production setup, this inventory allows management to reduce the number of setups.
To Meet Variations in Product Demand
If the demand for the product is known precisely, it may be possible (though not necessarily economical) to produce the product to exactly meet the demand. Usually, however, demand is not completely known, and a safety or buffer stock must be maintained to absorb variation.
Meet Customer Demand
Inventory allows a business to have goods or products readily available to meet customer demand in a timely manner. By maintaining an appropriate level of inventory, a company can ensure that customers can purchase what they need when they need it, thus improving customer satisfaction and loyalty.
To Allow Flexibility in Production Scheduling
A stock of inventory relieves the pressure on the production system to get the goods out. This causes longer lead times, which permit production planning for smoother flow and lower-cost operation through larger lot-size production. High setup costs, for example, favor producing a larger number of units once the setup has been made.
Smooth Production and Operations
Inventory is essential for ensuring smooth production and operations. It enables businesses to have the necessary raw materials, components, and supplies on hand to support the production process. This helps avoid delays or disruptions in manufacturing and allows for efficient scheduling and planning of production activities.
Buffer Against Supply Chain Uncertainties
Inventory acts as a buffer or safety stock against uncertainties in the supply chain. It helps mitigate risks associated with potential delays in the delivery of raw materials or components from suppliers. By having inventory on hand, a business can continue its operations even if there are disruptions or unforeseen events in the supply chain.
Take Advantage of Economies of Scale
Maintaining inventory can enable businesses to take advantage of economies of scale in production and procurement. By purchasing or producing in larger quantities, companies can often achieve lower costs per unit, reducing the overall cost of goods sold and increasing profitability.
Support Seasonal or Cyclical Demand
Inventory allows businesses to prepare for and meet seasonal or cyclical fluctuations in demand. For example, retailers stock up on inventory before the holiday season to accommodate the higher sales volume. Having inventory readily available during peak periods ensures that customers can be served promptly and maximizes sales opportunities.
Enable Quick Order Fulfillment
Inventory enables businesses to fulfill customer orders quickly, especially for products with short lead times or fast delivery expectations. By having inventory on hand, businesses can minimize order processing and delivery time, improving customer satisfaction and competitiveness.
Flexibility in Pricing and Promotions
Having inventory gives businesses the flexibility to implement pricing strategies and promotional campaigns. For instance, offering discounts, special offers, or bundle deals becomes feasible when there is sufficient inventory to support such initiatives. This can help attract customers, increase sales, and drive revenue.
Hedge Against Price Volatility
In certain industries or for certain commodities, inventory can serve as a hedge against price volatility. By purchasing and holding inventory at current prices, businesses can protect themselves from potential price increases in the future, thereby reducing the impact on their cost of goods sold.
Supply Chain Optimization
Inventory plays a role in optimizing the supply chain by balancing the timing and flow of goods. It allows for effective coordination between suppliers, manufacturers, and distributors, ensuring a smooth flow of products from production to customer delivery.
Strategic Value
Inventory can have strategic value, particularly for businesses with unique or exclusive products. Maintaining inventory of such products can create a sense of scarcity, exclusivity, and brand differentiation, leading to increased customer interest and perception of value.
To Take Advantage of Economic Purchase Order Size
There are costs to place an order: labor, phone calls, typing, postage, and so on. Therefore, the larger each order is, the fewer the orders that need to be written. Also, shipping costs favor larger orders—the larger the shipment, the lower the per-unit cost.
Many Other Domain-specific C Reasons
Depending on the situation, inventory may need to be carried out. For example, in-transit inventory is material being moved from the suppliers to customers and depends on the order quantity and the transit lead time. Another example is inventory that is bought in anticipation of price changes such as fuel for jet planes or semiconductors for computers.
Inventory Cost
Inventory cost refers to the expenses incurred by a business in acquiring, holding, and managing its inventory. It includes various components that contribute to the overall cost of inventory. Here are some key inventory cost elements:
Holding Costs
This broad category includes the costs for storage facilities, handling, insurance, pilferage, breakage, obsolescence, depreciation, taxes, and the opportunity cost of capital. Obviously, high holding costs tend to favor low inventory levels and frequent replenishment.
Setup Costs
Making each different product involves obtaining the necessary materials, arranging specific equipment setups, filling out required papers, appropriately charging time and materials, and moving out the previous stock of material.
If there were no costs or loss of time in changing from one product to another, many small lots would be produced. This would reduce inventory levels, resulting in savings in cost. One challenge today is to try to reduce these setup costs to permit smaller lot sizes.
Ordering Costs
These costs refer to the managerial and clerical costs to prepare the purchase or production order. Ordering costs include all the details, such as counting items and calculating order quantities. The costs associated with maintaining the system needed to track orders are also included in ordering costs.
FAQs About the What is Inventory?
What is the meaning of inventory?
Inventory is an idle stock of physical goods that contain an economic value, and are held in various forms by an organization in its custody awaiting packing, processing, transformation, use, or sale at a future point in time.
What is the purpose of inventory?
These are the following purpose of inventory:
1. To Maintain Independence of Operations
2. To Meet Variations in Product Demand
3. Meet Customer Demand
4. To Allow Flexibility in Production Scheduling
5. Smooth Production and Operations
6. Buffer Against Supply Chain Uncertainties
7. Take Advantage of Economies of Scale
8. Support Seasonal or Cyclical Demand
9. Enable Quick Order Fulfillment
10. Flexibility in Pricing and Promotions.