Table of Contents
- 1 What is Inventory?
- 2 Definition of Inventory
- 3 What is Inventory Management?
- 4 Definition of Inventory Management
- 5 Types of Inventories
- 6 Need for Inventory Management
- 7 Objectives of Inventory Management
- 8 Techniques of Inventory Management
- 9 Factors Affecting Inventory Management
- 10 FAQs About the Inventory Management
What is Inventory?
Inventory refers to the goods or materials that a business holds for the ultimate goal of resale (in the case of a product business) or repair (in the case of a service business). Inventory management is a crucial aspect of running a successful business, as it involves the constant monitoring of inventory levels, sales, purchases, and production processes.
Inventories are assets of the firm, and as such they represent an investment. Because such investment requires a commitment of funds, managers must ensure that the firm maintains inventories at the correct level. If they become too large, the firm loses the opportunity to employ those funds more effectively.
Similarly, if they are too small, the firm may lose sales. Thus, there is an optimal level of inventories and there is an economic order quantity model for determining the correct level of inventory.
Inventories, like receivables, are a significant portion of most firms’ assets and, accordingly, require substantial investments. To keep these investments from becoming unnecessarily large, inventories must be managed efficiently. In this lesson, we shall discuss how to do that and how efficient management of inventory is related to financial management.
Definition of Inventory
These are some simple definitions of inventory by authors:
[su_quote cite=”S.E. Bolten”]Inventory can be defined as “The term ‘Inventory’ refers to the stockpile of the product, a firm is offering for sale and the components that make up the product.[/su_quote]
[su_quote cite=”The Accounting Research and Terminology Bulletin”]The term inventory as “The aggregate of those items of tangible personal property which:[/su_quote]
- Are held for sale in the ordinary course of business,
- Are in the process of production for such sales,
- Are to be currently consumed in the production of goods or services to be available for sale.
[su_quote cite=”CIMA”]The function of ensuring that sufficient goods are retained in stock to meet all requirements without carrying unnecessarily large stocks.[/su_quote]
The following items are included in the inventory:
-
Raw Materials: These are goods that have not yet been committed to production in a manufacturing firm i.e. stored for use in future production.
-
Works-in-Progress: This category includes those materials that have been committed to the production process but have not been completed at the end of a financial year. Thus, these are neither raw materials nor finished goods.
-
Finished Goods: These are completed products awaiting sale. For a trading concern inventory always means finished goods, while for a manufacturing firm, they are the final output of the production process.
- Consumables and Stores: Loose tools, cotton, lubricant, oil, grease, etc. which are required for running and maintenance of plant and machinery are called consumables and stores. Though these are not held for sale but have significant importance.
The problems of managing inventories in manufacturing enterprises are relatively complex.
What is Inventory Management?
The area of inventory management covers the following individual phases: determining the size of inventory to be carried and lot sizes for new orders, establishing timing schedules and procedures, ascertaining safety levels, providing proper storage facilities, coordinating inventory policies with sales and production, arranging the procurement and disbursement of materials, record keeping, assigning responsibilities for carrying out the inventory control functions and providing necessary reports for supervising the overall activity.
Within these individual phases of acquisition, Unit/physical control i.e. material handling and production-related decisions are made by persons within purchasing and production departments.
The financial executive is only one of the persons in top management who is concerned with the levels and fluctuations of investment in inventories. He is concerned with any aspect of inventory management that is controllable from the standpoint of reducing inventory costs and risks. This is also called value control.
Definition of Inventory Management
These are some simple definitions of inventory management by authors:
[su_quote cite=”R. H. Ballou”]Inventory management is the set of policies and controls that monitor levels of inventory and determines what levels should be maintained, when stock should be replenished, and how large orders should be.[/su_quote]
[su_quote cite=”J. R. Stock and D. M. Lambert”]Inventory management concerns the balance between replenishment lead time, carrying costs of inventory, asset management, inventory forecasting, inventory valuation, inventory visibility, future inventory price forecasting, physical inventory, available physical space for inventory, quality management, replenishment, returns, and defective goods, and demand forecasting.[/su_quote]
[su_quote cite=”Dr. V. V. Sople”]Inventory Management deals with the management of stock either on a value or quantity basis. Planning, entry, and keeping records of all the products coming under the roof of an organization are the basics of inventory management. Proper management and control over them are important to reduce the cost of production.[/su_quote]
[su_quote cite=”Adam M. Grant and Peter T. Ward”]Inventory management is the ongoing process of moving parts and products into and out of a company’s location(s). Companies manage their inventory on a daily basis as they place new orders for products and ship orders out to customers.[/su_quote]
These definitions essentially address the same core principles but from slightly different perspectives. At its core, inventory management is about maintaining a balance between stock availability and the costs of holding and managing inventory.
Types of Inventories
Inventories are goods held for eventual sale by the firm and the raw materials or other components being used in the manufacturing of such goods. A retailer keeps an inventory of finished goods to be offered to customers whenever demanded them.
On the other hand, a manufacturing concern has to keep a stockpile of not only the finished goods it is producing but also all physical ingredients being used in the production process. The common types of inventories for most business firms may be classified:
- Finished Goods
- Work-in-Process
- Raw Materials
- MRO Inventory
- Transit Inventory
- Buffer Inventory or Safety Stock
- Cycle Inventory
- Anticipation Inventory
- Decoupling Inventory
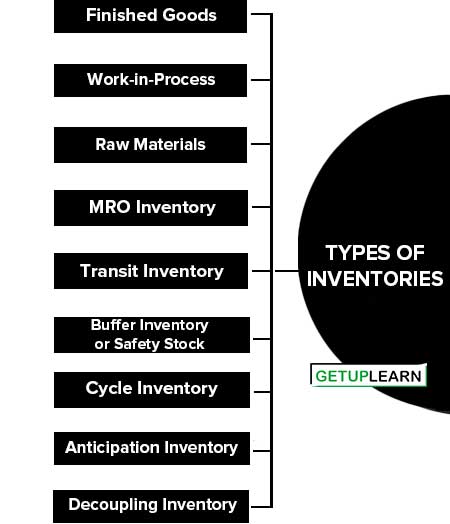
Finished Goods
These are completed products awaiting sale. They are the final output of the production process in a manufacturing firm. In the case of wholesalers and retailers, they are generally referred to as merchandise inventory.
Work-in-Process
Work-in-process refers to the raw materials engaged in various phases of the production schedule. The degree of completion may be varying for different units. Work-in-progress refers to partially produced goods. The value of work-in-process includes the raw material costs, the direct wages and expenses already incurred, and the overheads, if any.
Raw Materials
These are goods that have not yet been committed to the production process in a manufacturing concern. They may consist of basic raw materials or finished components.
MRO Inventory
MRO (Maintenance, Repair, and Operations) Inventory: This type of inventory includes items that support the production process and help maintain the business and its equipment. It can include items like cleaning supplies, lubricants, gloves, etc.
Transit Inventory
Also known as transportation inventory, this is inventory that is currently being moved from one location to another. For example, a shipment of goods being delivered from a manufacturer to a retailer.
Buffer Inventory or Safety Stock
This is extra inventory kept on hand to guard against variability in market demand and lead time. In other words, it serves as a buffer between the company and potential stockouts or shortages.
Cycle Inventory
This is the inventory that’s used during a single cycle of an operation. It’s the amount of inventory needed to fulfill customer demand during the period between reorders.
Anticipation Inventory
This is inventory that is held in excess of current demand to guard against forecasted increases in demand, often due to seasonal or cyclical fluctuations, or expected supply disruptions.
Decoupling Inventory
This type of inventory allows work centers within a production facility to operate independently.
Need for Inventory Management
Essentially, inventory is kept on hand to facilitate transactions. What is inventory today will be consumed tomorrow. A business can’t guarantee continuous production without maintaining sufficient raw material inventory.
Holding inventories allows a company to distinctively manage the purchasing, manufacturing, and selling processes. The following are the need for inventory management:
- Avoid Losses of Sale
- Gaining Quantity Discounts
- Continuity in Production
- Low Ordering Cost
- To Meet Contingencies
- Optimum Utilization of Resources
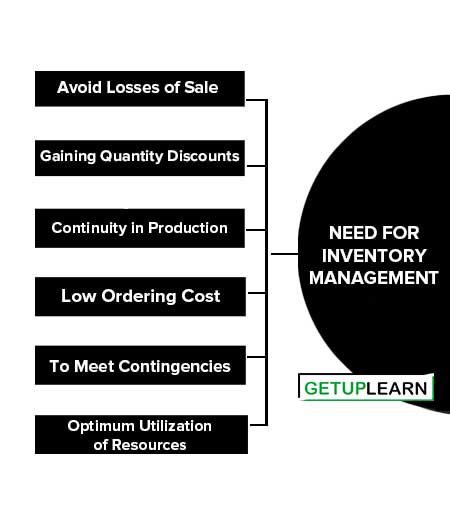
Avoid Losses of Sale
Inadequate inventory may disturb the production function and resulting the firm may not be in a position to deliver the goods within the scheduled time to its customers and it may lose customers forever.
The ability of the firm to give quick service and provide prompt delivery is closely tied to the proper management of inventory.
Gaining Quantity Discounts
If a firm is willing to maintain a large inventory in selected product lines, it may be able to make bulk purchases of goods at a heavy discount. Suppliers frequently offer a greatly reduced price if the firm orders double or triple its normal order.
By paying less for its goods, the firm can increase profits, as long as the costs of maintaining the inventories are less than the amount of the discount.
Continuity in Production
Inadequate inventory may cause production interruption and inefficiencies. It is very difficult to procure raw material whenever it is needed. If the firm has scheduled a long run and begins production, only due to a shortage of a vital raw material, the production may be halted at considerable cost to the firm.
So it is necessary to maintain an adequate level of inventory to continue the production process without any interruption.
Low Ordering Cost
Every time a firm places an order it incurs certain costs. The variable cost associated with individual orders can be reduced if the firm places a few large rather than numerous small orders.
To Meet Contingencies
Inventory is also held as a precaution or as a contingency for an increase in lead time or consumption rate. This increase may be due to suppliers’ strikes, labor strikes, transporters’ strikes, short supplies or bulk orders, etc.
Optimum Utilization of Resources
In a manufacturing concern production planning can be done with an object to have optimum utilization of resources namely men, machines, and materials. This objective can be achieved only if we hold sufficient inventory.
Objectives of Inventory Management
Inventory management covers a large number of issues including fixation of minimum and maximum levels; determining the size of the inventory to be carried; deciding about the issue price policy; setting up receipt and inspection procedure; determining the economic order quantity; and providing proper storage facilities. However, the firm is faced with the problem of meeting two conflicting needs while dealing with these issues.
The following are the objectives of inventory management:
- To have stocks available as and when they are required.
- To utilize available store space, but prevent stock levels from exceeding space availability.
- To meet a high percentage of demand without creating excess stock levels. In other words, “Neither to over-stock nor to run out” is the best policy.
- To provide, on an item-by-item basis, for re-order points and order such quantity as would ensure that the aggregate results conform with the constraints and objectives of inventory control.
- To decide which item to stock and which item to procure on demand.
- To ensure an adequate supply of materials, stores, spares, etc, minimize stockouts and shortages; and avoid costly interruption in operations.
- To enable the management to make costs and consumption comparisons between operations and periods.
- Minimizing the inventory carrying costs.
- To ensure investment in inventories at the optimum level.
Techniques of Inventory Management
Effective inventory management requires effective control over inventories. Inventory control refers to a system that ensures the supply of the required quantity and quality of inventories at the required time and prevents unnecessary investment in inventories. The techniques of inventory management are as follows:
- Determination of Economic Order Quantity
- Determination of Optimum Production Quantity
- ABC Classification
- Ratio Analysis in Inventory Management
- Aging Schedule
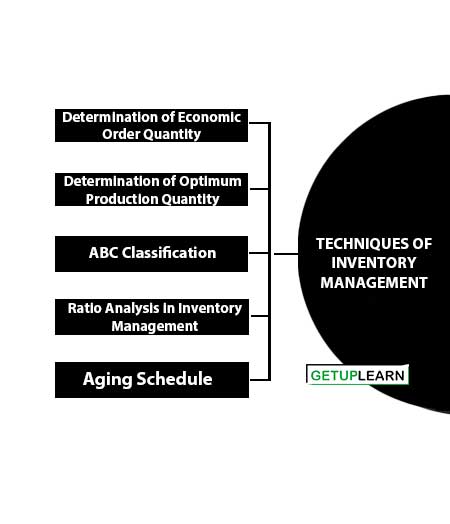
Determination of Economic Order Quantity
Determination of the quantity for which the order should be placed is one of the important problems concerned with efficient inventory management. If the firm is buying raw materials, it has to decide on lots in which it has to be purchased on each replenishment.
Determining an optimum inventory level involves two types of costs : (a) ordering costs and (b) carrying costs. The economic order quantity is the inventory level which minimizes the total ordering and carrying costs.
Determination of Optimum Production Quantity
The use of the EOQ model can be extended to production runs to determine the optimum size of manufacture. Two costs involved are ordering costs (set-up costs) and carrying costs. Production costs or set-up costs will reduce with bulk production runs.
But carrying costs will increase as large stocks of manufactured inventories will be held. The economic production size will be the one where the total set-up and carrying costs are minimum.
ABC Classification
An ABC analysis offers an important solution to the problem of scientific planning and control of inventories and is an important technique of inventory management. It is based on the value of different items constituting an inventory.
It may be concerned with several items raw materials, purchases and self-fabricated component parts, sub-assemblies, factory supplies, office supplies, tools, machinery, and handling equipment items. An inventory may be differentiated on the basis of bulk, size, weight, usage, value, durability, availability, etc., and should be controlled with due weightage to differential characteristics.
The idea underlying an ABC analysis is in this recognition of the principle that some items of inventory are more important than others. Thus, items are classified under broad categories -A, B, and C. The ABC technique enables an enterprise to keep its investment low and avoid stock-outs of critical items. Its objective is to reduce the minimum stock as well as the working stock.
Ratio Analysis in Inventory Management
Inventory turnover ratios are also calculated to minimize the investment in inventories. The turnover ratio can be calculated regarding each item of inventory on the basis of the following formula:
Cost of goods consumed/sold during the period Inventory Turnover Ratio = ——————————————————- Average inventory held during the period |
Aging Schedule
Classification of the inventories according to age also helps in identifying inventories that are moving slowly into the production of sales. This requires identifying the date of purchase/manufacture of each item in the inventory.
Factors Affecting Inventory Management
Several factors can significantly influence inventory management, impacting a company’s ability to effectively maintain and control its stock levels. Here are some of the main factors affecting inventory management:
- Nature of Product
- Nature of Business
- Terms of Purchase
- State of Economy
- Inventory Turnover Rate
- Value of the Product
- Attitude of Management
- Other Factors
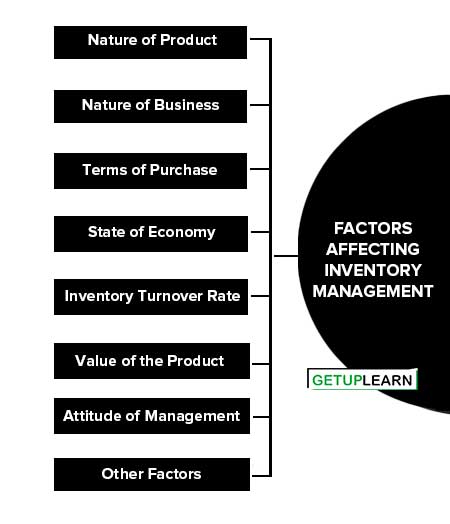
Nature of Product
The nature of the product greatly affects the quantity of inventory, like in the case of perishable and fashion goods. It is not feasible to store large quantities. If the firm deals in such types of products for which raw material is available only in a particular season, then the organization has to invest a huge fund in the season.
Nature of Business
If the business deals with luxury and consumer products, then it may maintain a lower level of inventory. But if it deals with industrial goods it has to maintain a higher level of inventory.
Terms of Purchase
If the supplier provides heavy discounts and liberal credit facilities on bulk purchases, then the firm may maintain a high level of inventory. Similarly, if supply conditions are favorable, with no disturbance in the supply chain then the inventory level can be low, but in adverse conditions or uncertainty, the firm should maintain a high level of inventory.
State of Economy
In the case of the booming economy, the firm will maintain a high level of inventory to grab the high chances of emerging large orders and vice-versa.
Inventory Turnover Rate
When the turnover rate is high, investment in inventories tends to be low and vice-versa.
Value of the Product
In the case of high-value products, the firm cannot afford to have a large inventory. In the case of low-value products, the firm can keep large quantities in stock.
Attitude of Management
Conservative management does not bother much with forecasting, or demand and consider it safer to carry large stocks, while energetic or dynamic manager decides this by using advanced techniques of forecasting.
Other Factors
Many other factors like market structure, fluctuations in the price level, availability of funds, government policies, period of operating cycle, etc. also affect the level of inventories.
FAQs About the Inventory Management
What is the definition of inventory?
Inventory can be defined as “The term ‘Inventory’ refers to the stockpile of the product, a firm is offering for sale and the components that make up the product. By S.E. Bolten
What is the definition of inventory management?
Inventory management is the set of policies and controls that monitor levels of inventory and determines what levels should be maintained, when stock should be replenished, and how large orders should be. By R. H. Ballou
What are the types of inventories?
These are the 9 types of inventories:
1. Finished Goods
2. Work-in-Process
3. Raw Materials
4. MRO Inventory
5. Transit Inventory
6. Buffer Inventory or Safety Stock
7. Cycle Inventory
8. Anticipation Inventory
9. Decoupling Inventory.
What is the need for inventory management?
The need for inventory management are:
1. Avoid Losses of Sale
2. Gaining Quantity Discounts
3. Continuity in Production
4. Low Ordering Cost
5. To Meet Contingencies
6. Optimum Utilization of Resources.
What are the techniques of inventory management?
These are the following methods or techniques of inventory management:
1. Determination of Economic Order Quantity
2. Determination of Optimum Production Quantity
3. ABC Classification
4. Ratio Analysis in Inventory Management
5. Aging Schedule.
What are the factors affecting inventory management?
The factors affecting inventory management:
1. Nature of Product
3. Nature of Business
4. Terms of Purchase
5. State of Economy
6. Inventory Turnover Rate
7. Value of the Product
8. Attitude of Management
9. Other Factors.