Table of Contents
Advantages of Logistics Management
Logistics is the sum total of materials management and distribution in any process. It includes the whole gamut of activities right from order processing to delivery of goods and services.
In this context, logistics find a place in a series of activities in any business process. The advantages of logistics in any business process can be summarized below:
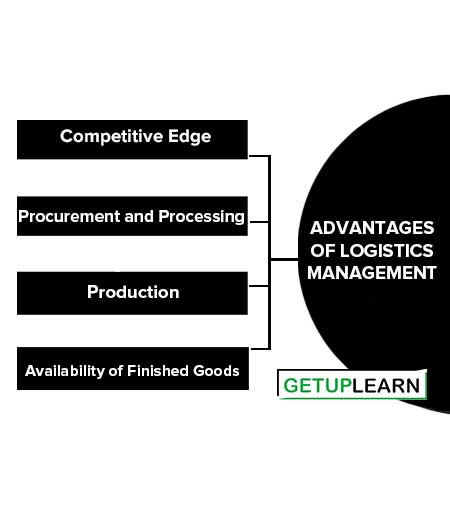
Competitive Edge
Logistics is the enabler for providing products and services with a minimum of time and cost. This is possible by virtue of a robust scheduling mechanism whereby all of its components work in unison to ensure timeliness and effectiveness. Scheduling is the amalgamation of sequencing, routing, dispatching, and expediting.
Procurement and Processing
Logistics ensures a smooth process for procurement of raw materials, and supplies from vendors with the timely delivery of the supplies at the shop floor to facilitate uninterrupted timeliness in production.
Handling of materials received, necessary quality checks, onward movement of the materials, storage prior to production, and post-production are done under the umbrella of logistics.
Production
Logistics ensures a smooth production process by managing the flow of inventory on the shop floor, scheduling of material, temporary packaging wherever required, and material handling. Logistics helps to reduce if not eliminate idle time of material and the machinery at hand.
Availability of Finished Goods
Finished goods are marketed, and sold efficiently by virtue of logistics. Logistics arranges for adequate packaging, transportation, and distribution of goods to the customers’ end. It facilitates the matching of supply and demand requirements by the distribution function through inventory management systems.
Elements of Logistics Management
Some of the major elements of logistics management are:
- Customer Order Processing
- Inventory Management in Logistics
- Material Handling
- Packaging
- Transportation
- Warehousing
- Customer Service
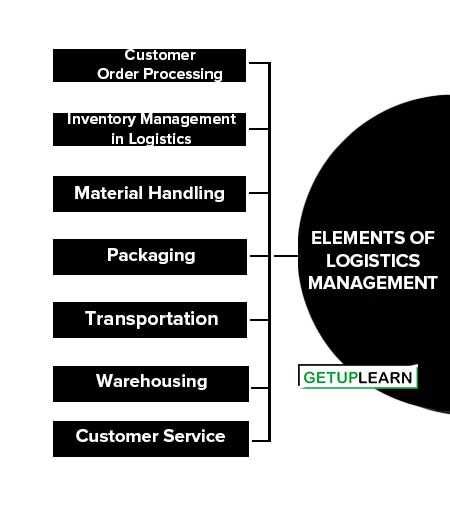
Customer Order Processing
The trigger for logistics is customer order processing. Forecasts of orders and placed orders necessitate the process to facilitate the delivery of finished goods at the customers’ end. The instant of receiving the order initiates order processing at the producers’ end.
The process begins with orders and necessitates activities for the delivery of the products to customers. The functions of order processing are precisely four viz., order receiving, order handling, order picking, and order fulfillment.
Inventory Management in Logistics
The instant at which an order is received initiates the management of inventory at different stages. The flow of inventory in the form of raw materials from vendors to manufacturers to distributors and finally at the customer’s end is a continuous process. The variation is the type and form of inventory at different stages.
The difficulty in accurate matching of demand and supply necessitates inventory holding in the different stages. Reasons for the gap in are plenty; unavailability of accurate demands, production halts, sudden changes in tastes and preferences, etc. Inventories exist in different forms including raw materials, sub-assemblies, work-in-progress or finished goods.
Previously inventory used to be accumulated at all stages to compensate for uncertainties in orders received and to prevent stockouts. However, owing to the influence of information technology and advanced managerial practices like Just-in-time (JIT), Total Quality Management, and lean manufacturing, firms now operate with absolute zero levels of inventory.
Material Handling
Material handling encompasses the set of activities wherein all activities pertaining to the movement of movement, packaging, and storing of inventory of different forms at different stages. It ensures an uninterrupted flow of raw materials from sources for processing and of finished goods to the customers’ end.
Objectives of Material Handling:
- An uninterrupted flow of goods.
- Reduction of time of delivery of goods.
- Checking damage and wastage of items in packaging and transit.
- Reduced cost of handling
Packaging
Packaging is the entire process through which a product is enclosed for delivery to the customers. It is inclusive of the physical cover of the product to safeguard the contents within till it reaches the end customer.
Packaging goes ahead to draw the attention of prospective customers and to enable ease of handling during transit. The purpose is not merely to provide a protective capsule but to present it in a form that adds to customer delight through visual appeal. Functions of Packaging in logistics parlance are:
- To protect the materials from damages of transit and storage.
- To provide adequate protection from shocks and vibrations that happen during travel.
- To facilitate the ease of stackability of inventory using minimal space.
- To facilitate equal distribution of weight within the packages for automated handling equipment.
- To provide ease of handling to items requiring special care as those which are fragile or susceptible to damage in case of improper handling.
For fulfilling the functions stated, the various types of packaging used are tetra packs, corrugated boxes, wooden pallets, metal and alloy cans, plastic films, etc.
Transportation
Transportation in logistics is the movement of goods all along from the source (of raw materials) to the end user. It is not merely the carrier of goods in different forms, but the process that makes raw materials available at the source of production, the flow of semi-finished goods, and the availability of finished goods at the right place, time, and quantities.
The objective of transportation is to make availability of goods efficiently satisfying the customer demand by virtue of economies of scale in the flow process. Transportation uses different modes like roadways, railways, seaways, and airways. Sometimes more than one mode is used when it is called multi-modal transportation.
Warehousing
The flow of inventory of different forms from the source to the customers’ end is a continuous process but with stoppages at the storehouse. Raw materials waiting to be processed or assembled or finished goods waiting to be received by customers all need temporary storage arrangements.
This process of providing temporary waiting arrangements is called warehousing. The purpose of warehousing is to ensure storage of the inventory preserving its characteristics and protecting it from physical damages. Warehouses are also used for aggregation of products from different production sites before dispatching to markets, and sorting of products for different geographical locations.
Customer Service
A customer in operations management is one who buys an end product or avails a service for his/her own consumption or for the consumption of someone else. The product (or the service) is an outcome of a sequence of value-added activities.
Customer service is a process by which value-added services, which may be products or services, are made available to the customers by virtue of a demand created in the market by the customer or through a strategy of the firm to push its products (or services) to the market for sale. The process begins with an order or a demand forecast data and completes with a trade-off between cost and the service of the same.
FAQs About the Elements of Logistics Management
What are the advantages of logistics management?
The advantages of logistics management:
1. Competitive Edge
2. Procurement and Processing
3. Production
4. Availability of Finished Goods.
What are the elements of logistics management?
The elements of logistics management are: 1. Customer Order Processing 2. Inventory Management in Logistics 3. Material Handling 4. Packaging 5. Transportation 6. Warehousing 7. Customer Service.