Table of Contents
- 1 Meaning of Inventory Management
-
2 Types of Inventory
- 2.1 Production Inventories
- 2.2 MRO Inventories
- 2.3 In-Process Inventories
- 2.4 Finished-Goods Inventories
- 2.5 Transaction Inventory
- 2.6 Speculative Inventory
- 2.7 Precautionary Inventory
- 2.8 Working Stock
- 2.9 Safety Stock
- 2.10 Anticipation Stock
- 2.11 Pipeline Stock
- 2.12 Decoupling Stock
- 2.13 Psychic Stock
- 3 Inventory Control Techniques
- 4 Approaches to Inventory Management
- 5 FAQs About the Types of Inventory
Meaning of Inventory Management
Inventory management refers to efficient control over the stock of goods stored in the warehouse for the purpose of meeting customer demands in time. In order to keep minimum inventory cost, an organization has to go for an optimum inventory which requires an accurate sales forecast.
A number of techniques have been developed that help organizations in deciding the volume of inventory.
Types of Inventory
There are several ways in which inventories are classified. These are the two bases for types of inventory:
- Production Inventories
- MRO Inventories
- In-Process Inventories
- Finished-Goods Inventories
- Transaction Inventory
- Speculative Inventory
- Precautionary Inventory
- Working Stock
- Safety Stock
- Anticipation Stock
- Pipeline Stock
- Decoupling Stock
- Psychic Stock
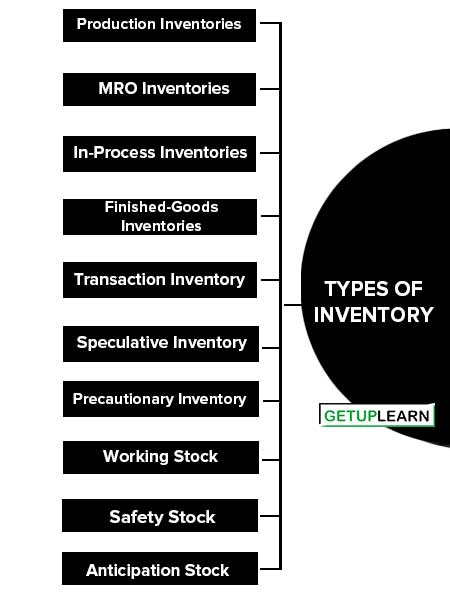
On the Basis of the Nature of Materials:
Production Inventories
Raw materials, parts, and components that are consumed in the production process of goods come under the category of production material inventories.
MRO Inventories
Maintenance, repair, and operating (MRO) items that are used in the production process but do not become a part of the products, are called MRO items and their stocking is called MRO inventories.
In-Process Inventories
These goods are partially completed or finished that are still in the production operation, i.e. semi-finished products found at various stages in the production process are called in-process inventories.
Finished-Goods Inventories
These inventory items are final products, available for sale and distribution, i.e. completed products ready for shipping. This type of inventory is a major concern for the physical distribution system.
On the Basis of Uses of Materials:
This categorization is more useful for physical distribution management, which is listed as:
Transaction Inventory
This type of inventory item is basically needed for transactions, e.g., transactions of finished saleable products or raw materials.
Speculative Inventory
The stocking of materials is a measure of speculation so as to get greater prices for the goods in the future.
Precautionary Inventory
The stocking of certain materials or items to prevent the breakdown of the production process and/or to meet any unexpected demand.
Another way to explain the purposes of inventory services is by introducing functional classifications of inventory. Based on their utility, all inventories can be placed in one or more of the following categories:
Working Stock
Working stock is also known as a cycle or lot-size stock. In general, it is an average amount of inventory in stock that results from lot sizes to get the benefits of minimum ordering and holding costs, quantity discounts, and/or favorable freight rates.
Safety Stock
The safety stock or buffer stock function of an inventory is to meet short-range variations in either demand or replenishment, i.e. safety stock inventory is held in stock to protect against the uncertainties of demand and supply.
Anticipation Stock
The anticipation or seasonal or stabilization stock refers to holding a high level of inventory to meet the peak seasonal demand, erratic requirements, or inconsistency in the production capacity, e.g. production and holding of woolen garments in advance to meet the demand during winter.
Pipeline Stock
The pipeline stock is also known as transit stock or work-in-process inventory. Generally, a geographical gap exists between the point of production and the point of consumption of goods.
Hence, goods in transit from the manufacturer to be delivered to a customer are called pipeline stock. Furthermore, raw materials and components being processed, waiting to be processed, or being moved to become finished goods also come under the functions of pipeline inventory function.
Decoupling Stock
Decoupling stock is inventory accumulated between the various departments’ activities (manufacturers, wholesalers, retailers, etc.) or stages to reduce the requirement for completely synchronized operations. In other words, inventory brings about a smooth interface between the material, production, and distribution systems of an organization.
Psychic Stock
Psychic stock refers to a window display of an inventory in order to stimulate demand and act as a salesman. This function of inventory generates an impulse-buying tendency, fulfilling the need for a promotion function.
Inventory Control Techniques
The ultimate objective of the inventory control program is to provide maximum customer service at a minimum cost. Traditionally, inventory management involved two fundamental questions: how much to reorder vendor and/or their plants and when to reorder.
Nowadays, questions regarding where inventory should be held and what specific items should be available at specific locations make inventory management a big challenge. Sople (2010) classified inventory control techniques into two groups.
Selective Inventory Control Techniques
In these methods, the degree of control varies with the importance of the item. Some of the commonly used inventory control techniques in the industry are:
- ABC Inventory Control Technique
- VED Inventory Control Technique
- SAP Inventory Control Technique
- FSN Inventory Control Technique
ABC Inventory Control Technique
It relates to the annual usage cost of a particular item. The items are classified as per the usage value. Items in class A are less in number (approx. 10 percent of total inventory) but cost approximately 60-70 percent of the total cost of inventory.
Items under class B cost 20-30 percent of total inventory cost as well as 20-30 percent in numbers and finally item C constitutes 60-70 percent of volume but less than 10 percent of inventory cost. It means activities that are considered high on priority are classified as A, those with lesser priorities are grouped under B and the group C items are having least priority.
VED Inventory Control Technique
It relates to the Vital, Essential, and Desirable status of the inventory items. As the term implies, certain items are considered to be vital for meeting operational requirements and this aspect is taken into consideration for making any inventory-related decisions.
SAP Inventory Control Technique
The scarce, Available, and Plenty status of an inventory item is used for planning and forecasting inventory requirements. The ordered quantity is governed by the scarcity factor.
FSN Inventory Control Technique
Fast, Slow, and Normal determine the consumption pattern of the items.
In all these control techniques, the degree of control varies with the importance of the items. For example, for the A class, Vital, Scarce, and Fast moving items perpetual reviews are recommended, while for the B class, Essential and Medium moving items periodic reviews will be OK. In the case of C class, Desirable and Slow moving items the periodicity of review will be longer.
Approaches to Inventory Management
The modern approaches for controlling the inventory are based on four primary factors, i.e., flow, flexibility, balancing, and integration:
- Materials Requirement Planning (MRP)
- Manufacturing Resource Planning (MRP II)
- Distribution Requirement Planning (DRP)
- Just-in-Time (JIT)
- Vendor Managed Inventory (VMI)
Materials Requirement Planning (MRP)
The materials requirement planning system (MRP) most commonly found in modern manufacturing or processing concerns is based on the Japanese Kanban system. MRP is a computerized inventory control system intended to minimize the investment in manufacturing/processing materials and components, consistent with matching production levels to current demand.
MRP is typically applied to manage inbound material movement in the organization and is based on production requirements and schedules.
Manufacturing Resource Planning (MRP II)
MRP II represented a move towards an integrated approach to the entire manufacturing process. It is defined as a method for the effective planning of all resources of a manufacturing organization. MRP and MRP-II systems draw on Master Production Schedule (MPS).
Distribution Requirement Planning (DRP)
Distribution Requirement Planning (DRP) applies the techniques of MRP II to warehousing and transportation activities.
It is guided by customer demand and allocates inventory from the mother warehouse to the various distribution centers based on various factors such as demand patterns, safety stock provisions, order quantity, reorders point, average performance cycle length, etc. DRP also coordinates finished goods requirements across the distribution network.
Just-in-Time (JIT)
The purpose of JIT is to eliminate all production activities which do not directly add value to the product. The just-in-time (JIT) concept was developed with manufacturing in mind but it has implications for distribution.
Whilst the organizations that have implemented this system tend to be large enterprises, the system also has implications for the smaller and middle-sized firms that may be their competitors, suppliers, or customers. JIT has four specific objectives:
- The production of goods that the customer wants
- The production of goods when the customer wants them
- The production of perfect quality goods
- The elimination of waste (in labor, inventory movement, space, etc.).
Vendor Managed Inventory (VMI)
It is made popular by Bose Incorporation. In VMI, the supplier takes charge of inventory management of products and manages the replenishment process based on the consumption pattern of the customer. For VMI to be successful, three things are essential, i.e., the right partners, the right set of products, and mutual trust.
FAQs About the Types of Inventory
What are the types of inventory?
The following are the types of inventory: 1. Production Inventories 2. MRO Inventories 3. In-Process Inventories 4. Finished-Goods Inventories 5. Transaction Inventory 6. Speculative Inventory 7. Precautionary Inventory 8. Working Stock.
What are the inventory control techniques?
Some of the commonly used inventory control techniques in the industry are:
1. ABC Inventory Control Technique
2. VED Inventory Control Technique
3. SAP Inventory Control Technique
4. FSN Inventory Control Technique.