Table of Contents
Techniques of Scientific Management
Taylor and his close associates suggested the following techniques of Scientific Management in order to put it into practice:
- Separation of Planning and Doing
- Functional Foremanship
- Job Analysis
- Standardization
- Scientific Selection and Training
- Differential Piece Wage Plan
- Economy
- Mental Revolution
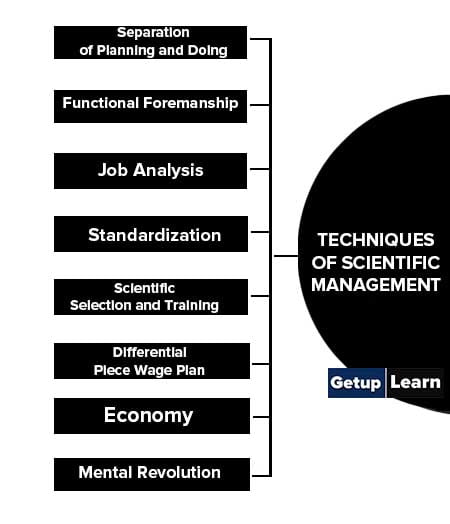
Separation of Planning and Doing
Taylor emphasized the need for planning work to be performed and he wanted the planning function to be separated from the executive function.
Before Taylor’s scientific management, both planning and execution were carried out by the same individual and there was only a supervisor to control the job. This led to a lot of confusion and Taylor wanted the planning activity to be done separately by the planning department, where the worker had no role to play.
Functional Foremanship
Taylor developed a theory of functional authority called functional foremanship based on the specialization of functions. Here planning was separated from executing. In this system, eight foremen were involved to direct and control the activities of the workers.
Of these, four were concerned with planning, namely, route clerk, instruction card clerk, time and cost clerk, and shop disciplinarian. The remaining four were concerned with getting the required performance from the workers, namely gang boss, speed boss, repair boss, and inspector.
Job Analysis
It is undertaken to find out the best possible way to do a particular activity. Any activity that requires minimum movements and consequently less cost and time is the best way of doing that activity or job. This can be determined by taking up time–motion and fatigue studies.
Time Study
this is otherwise called work measurement. It helps in recording the time required to do each element of an industrial operation. Thus, the precise time for each operation is clearly laid down. This helps in fixing fair and standard work for a period.
Motion Study
It helps in studying the movement of an operator or machine. Here, wasteful movements can be eliminated and the earliest method of doing a particular job can be determined.
Fatigue Study
Both physical, as well as mental fatigue, has an adverse effect on the worker’s performance and health. Fatigue study indicates the amount and frequency of rest required in completing the job.
Fatigue is normally caused because of continuous work without rest pauses, repetitive operations, poor working environment, etc. Fatigue study is to maintain operational efficiency of works. The concept of job analysis, as given by Taylor, suggests a fair day’s work requiring certain movements and rest pauses to complete it.
Standardization
Taylor suggested standardization of instruments and tools, amount of work, period of work, working conditions, cost system, and several other items. This would help to reduce wastage and spoilage of materials, reduce fatigue among the workers and improve the quality of work.
Standardization of activities and equipment should be fixed well in advance on the basis of job analysis and various elements of costs that are required for performing the work.
Scientific Selection and Training
According to Scientific Management workers should be scientifically selected taking into account their education, experience, skill, and physical strength so that the right man is put into the right job.
A person who is technically and physically fit for a given job should be assigned that work. Besides this, proper training should be given to make him efficient and perfect.
Differential Piece Wage Plan
Taylor applied the concept of a differential piece-wage plan in order to motivate and attract highly efficient workers. According to the plan, if a worker completes the normal work given to him, he will be given a higher piece rate.
On the other hand, one who does not complete gets a lower piece rate. Taylor also suggested that only individual performance should be taken into consideration.
Economy
The application of scientific management should always lead to economy and profitability. For this purpose, techniques of cost estimates and control should be adopted. By making effective use of resources, wastage can be eliminated, and thereby profitability and efficiency can be improved.
Scientific management should not be based only on technical and scientific aspects but due consideration should also be given to profit and economy.
Mental Revolution
The concept of the Mental Revolution laid down by Taylor calls for a change in the mental attitudes of the workers and the management towards each other. This change in mental attitude can be brought about through mutual cooperation and confidence.
No principle of scientific management can be applied without a revolutionary change in attitude. Mental Revolution can be obtained by:
- Taking proper efforts to increase production.
- Creating a spirit of mutual confidence and trust.
- Developing a scientific attitude towards problems. Mental Revolution helps in the effective accomplishment of organizational goals because both workers and management would turn their attention toward increasing the size of the surplus and will not be bothered about the division of surplus.
Taylor’s scientific management has provided a number of benefits to the industry. The main benefits are conservation and savings, better utilization of different resources, development of workers, and satisfaction of customer needs by providing quality products at lower prices.
What are the techniques of scientific management?
The following are the techniques of scientific management:
1. Separation of Planning and Doing
2. Functional Foremanship
3. Job Analysis
4. Standardization
5. Scientific Selection and Training
6. Differential Piece Wage Plan
7. Economy
8. Mental Revolution.