Table of Contents
- 1 What is Material Handling?
- 2 Objectives of Material Handling
-
3 Principles of Material Handling
- 3.1 Orientation Principle
- 3.2 Requirement Principle
- 3.3 Integrated System Principle
- 3.4 Standardization Principle
- 3.5 Just-in-time Principle
- 3.6 Unit-Load Principle
- 3.7 Minimum Travel Principle
- 3.8 Space Utilization Principle
- 3.9 Ergonomic Principle
- 3.10 Energy Principle
- 3.11 Ecology Principle
- 3.12 Mechanization Principle
- 3.13 Automation Principle
- 3.14 Flexibility Principle
- 3.15 Simplification Principle
- 3.16 Gravity Principle
- 3.17 Safety Principle
- 3.18 Computerization Principle
- 3.19 Systems Flow Principle
- 3.20 Layout Principle
- 3.21 Cost Principle
- 3.22 Maintenance Principle
- 3.23 Obsolescence Principle
- 3.24 Team Solution Principle
- 4 FAQs About the Material Handling
What is Material Handling?
Material handling is a very basic and internal component of any physical distribution system for the movement of goods. Generally, finished goods are often packed in consumer-sized boxes, bottles, or cans, which are handled either manually or by some small mechanical handling devices.
Whereas, raw materials or industrial products are often moved in bulk quantities and are loosely packed or unpacked, and handled by more advanced and big mechanical devices, such as pumps, conveyor belts, cranes, etc.
Material handling system has experienced major changes and improvements during the past few years. It represents all those activities that are responsible for the efficient movement of products within the factory, warehouses, and transportation company terminals.
In the past, the activity was mainly associated with manpower but at present, it is a mechanized activity for which improved conveyor systems and forklift equipment are used. The concept of containerization is equally responsible for the improvement of the physical distribution system.
The improvement in the process of physical distribution has also resulted in the reduction of material handling costs and time and the effectiveness of transportation and storage. At the same time, it contributes to customer service standards by expanding the process of order cycle and shipment.’
Objectives of Material Handling
The major objectives of material handling are:
- Reduction in wastage of machine and order picking times.
- Reduction in overall replenishment cycle time by quick marshaling and movement of goods.
- Uninterrupted production and distribution schedules for the avoidance of movement bottlenecks, such as loading and unloading problems.
- Protection of goods from breakages or damages during movements.
- Offering safety to workers and providing safer working conditions.
- Ensuring better customer service and satisfaction.
- Enhancing productivity and efficiency by reducing handling costs.
Principles of Material Handling
In order to achieve the above-stated objectives, the material handling system follows certain principles. Materials handling is a branch of engineering that deals with the movement of the material between two or more different points.
Most material handling systems are designed and tested through rigorous engineering analysis. The College Industry Council on Materials Handling Education has developed and refined a list of twenty-four principles of material handling (MHED, 1993-94), which are listed below:
- Orientation Principle
- Requirement Principle
- Integrated System Principle
- Standardization Principle
- Just-in-time Principle
- Unit-Load Principle
- Minimum Travel Principle
- Space Utilization Principle
- Ergonomic Principle
- Energy Principle
- Ecology Principle
- Mechanization Principle
- Automation Principle
- Flexibility Principle
- Simplification Principle
- Gravity Principle
- Safety Principle
- Computerization Principle
- Systems Flow Principle
- Layout Principle
- Cost Principle
- Maintenance Principle
- Obsolescence Principle
- Team Solution Principle
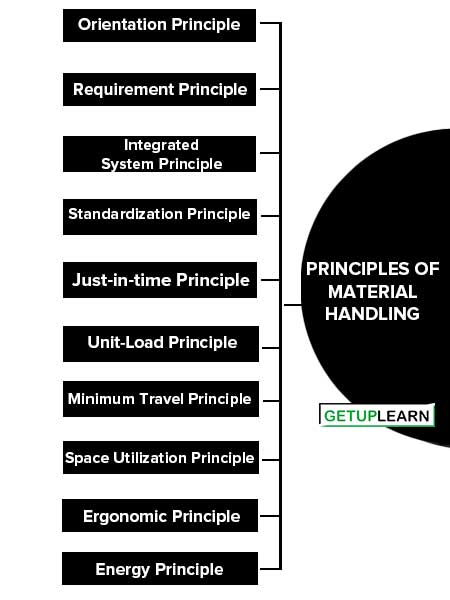
Orientation Principle
The orientation principle requires that one should look at the entire system first, to learn how and why it operates. One should also look at the relationships with other systems and also to physical limitations.
Requirement Principle
What the system is expected to do? The requirement principle focuses on answering this question.
Integrated System Principle
All storage and handling operations must be coordinated, and that is known as the integrated system principle.
Standardization Principle
The standardization principle stands for what the name suggests. It is important in the selection of packaging that is to be used. Other things being equal, it is advantageous to standardize as small a number of packages or wraps as possible.
Just-in-time Principle
The just-in-time principle holds that products are not moved until needed.
Unit-Load Principle
The unit-load principle conflicts with the just-in-time principle in that it emphasizes the importance of handling materials in large blocks, such as the unit loads mentioned earlier in the chapter.
Minimum Travel Principle
Systems should be set up so that loads move for the shortest distances; this is the minimum travel principle.
Space Utilization Principle
The space utilization principle requires one to make good use of space. Some materials handling equipment is designed to fit into otherwise underutilized space. Ergonomics involves an understanding of how the human body functions as it performs physical tasks.
Ergonomic Principle
The ergonomic principle is used to justify manufacturing and materials handling systems that protect workers from performing difficult and repetitive functions that ultimately result in injuries or disability.
Energy Principle
The energy principle aims at reducing energy consumption by the materials handling activities.
Ecology Principle
The ecology principle calls on devising systems that are environmentally friendly, with an example being the choice of materials to use in packaging.
Mechanization Principle
Using machines, where it is justified to replace human effort is called the mechanization principle.
Automation Principle
The automation principle involves the development of equipment that is pre-programmed, or self-controlled.
Flexibility Principle
The flexibility principle is important for those systems where there are changes from time to time in the tasks that the system is expected to perform.
Simplification Principle
The simplification principle means what it says: Avoid overly complicated systems.
Gravity Principle
The gravity principle is easy to understand; one should rely on gravity to move materials wherever possible.
Safety Principle
The safety principle emphasizes the importance of having equipment that is safe to operate and to be heard.
Computerization Principle
The computerization principle recognizes the widespread use of computers to operate both individual pieces of equipment and massive supply chains spread across several continents.
Systems Flow Principle
The systems flow principle calls for an orderly and logical flow of materials.
Layout Principle
The layout principle requires that the system be laid out in a manner that takes all these listed principles into account.
Cost Principle
The cost principle recognizes that all material handling alternatives have associated costs and that these costs must be carefully considered as the system is devised.
Maintenance Principle
Once in operation, a system must be maintained. This is recognized by the maintenance principle, which includes taking various maintenance alternatives into account.
Obsolescence Principle
The obsolescence principle recognizes that this equipment must be phased out, taking into account its usefulness, as well as tax and accounting considerations.
Team Solution Principle
The team solution principle means that material handling challenges are sufficiently large and complex and teams of people are often required to devise the best system.
A wide variety of materials handling equipment are used by different industrial sectors, depending on their needs and requirements.
FAQs About the Material Handling
What are the principles of material handling?
These are the principles of material handling: Orientation Principle, Requirement Principle, Integrated System Principle, Standardization Principle, Just-in-time Principle, Unit-Load Principle, Minimum Travel Principle, Space Utilization Principle, Ergonomic Principle, Energy Principle, and Ecology Principle.