Table of Contents
Features of Scientific Management
Taylor conducted various experiments at his workplaces to find out how human beings could be made more efficient by standardizing the work and better methods of doing the work. These experiments have provided the following features of scientific management:
- Separation of Planning and Doing
- Functional Foremanship
- Job Analysis
- Standardization
- Scientific Selection and Training of Workers
- Financial Incentives
- Economy
- Mental Revolution
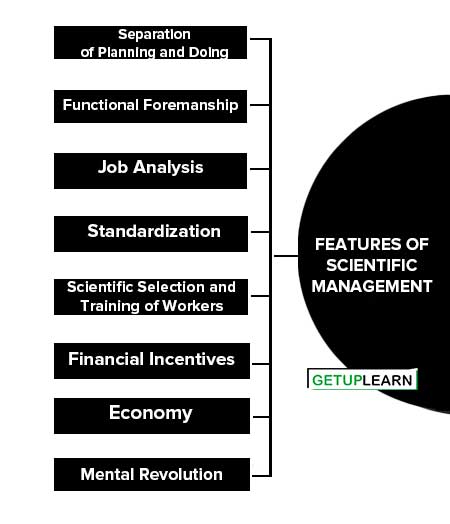
Separation of Planning and Doing
Taylor emphasized the separation of the planning aspect from the actual doing of the work. Before Taylor‘s scientific management, a worker used to plan how he had to work and what instruments were necessary for that.
The worker was put under the supervision of a supervisor commonly known as a gang boss. Thus supervisor‘s job was merely to see how the workers were performing. This was creating a lot of problems, and Taylor emphasized that planning should be left to the supervisor and the worker should emphasize only operational work.
Functional Foremanship
Separation of planning from doing resulted in the development of a supervision system that could take planning work adequately besides keeping supervision on workers. For this purpose, Taylor evolved the concept of functional foremanship based on the specialization of functions. In this system, eight persons are involved in directing the activities of workers. Out of these, four persons are concerned with planning:
- Route Clerk
- Instruction Card Clerk,
- time and Cost Clerk,
- Disciplinarian.
The remaining four persons are concerned with doing aspects of the work. These are:
- Speed Boss,
- Inspector,
- Maintenance Foreman,
- Gang Boss.
All of them give directions to workers on different aspects of work. This is against the unity of command principle
Job Analysis
Job analysis is undertaken to find out the best way of doing the thing. The best way of doing a job is one which requires the least movement, consequently less time and cost. The best way of doing the things can be determined by taking up time-motion-fatigue studies:
- Time study involves the determination of the time a movement takes to complete. The movement which takes minimum time is the best one. This helps in fixing the fair work for a period.
- Motion study involves the study of movements in parts that are involved in doing a job thereby eliminating the wasteful movements and performing only necessary movements. Elimination of unnecessary movements in doing work reduces the time taken in performing work and also the fatigue of workers.
- Fatigue study shows the amount and frequency of rest required to complete the work.
After a certain period of time, workers feel fatigued and cannot work at full capacity. Therefore, they require rest in between. When the rest is allowed, they start working at full capacity. This job analysis, as given by Taylor, suggests a fair amount of a day‘s work requiring certain movements and rest periods to complete it.
Standardization
As far as possible, standardization should be maintained with respect to instruments and tools, period of work, amount of work, working conditions, cost of production, etc. These things should be fixed in advance on the basis of job analysis and various elements of costs that go into performing a work.
Scientific Selection and Training of Workers
Taylor has suggested that workers should be selected on a scientific basis taking into account their education, work experience, aptitude, physical strength, etc.
A worker should be given work for which he is physically and technically most suitable. Apart from selection, proper emphasis should be given to the training of workers which makes them more efficient and effective.
Financial Incentives
Financial incentives can motivate workers to put in their maximum efforts. If provisions exist to earn higher wages by putting in extra effort, workers will be motivated to earn more. Taylor himself applied the concept of a differential piece rate system which was highly motivating.
According to this scheme, a worker who completes the normal work gets wages at a higher rate per piece and one who does not complete gets at a lower rate. Thus, there is a considerable difference in wages between those who complete the work and those who do not complete it.
To make the differential piece rate system work, Taylor has suggested that wages should be based on individual performance and not on the position he occupies. Further, the wage rate should be fixed on accurate knowledge and not on estimates.
Economy
While applying scientific management, not only scientific and technical aspects should be considered but adequate consideration should be given to economy and profit. For this purpose, techniques of cost estimates and control should be adopted.
The economy and profit can be achieved by making the resources more productive as well as by eliminating wastage. Taylor has clarified by giving examples of how resources are wasted by not following scientific management.
Mental Revolution
Scientific management depends on the mutual cooperation between management and workers. For this cooperation, there should be a mental change in both parties from conflict to cooperation. Taylor feels that this is the most important feature of scientific management because, in its absence, no principle of scientific management can be applied.
Principles of Scientific Management
Taylor has given certain basic principles of scientific management. The fundamental principles that Taylor saw underlying scientific management may be given below:
- Replacing Rule of Thumb with Science
- Harmony in Group Action
- Cooperation
- Maximum Output
- Development of Workers
Replacing Rule of Thumb with Science
Taylor has emphasized that in scientific management, organized knowledge should be applied which will replace the rule of thumb. While the use of the scientific method denotes precision in determining any aspect of work, the rule of thumb emphasizes estimation.
Since the exactness of various aspects of work like day‘s fair work, standardization in work, differential piece rate for payment, etc., is the basic core of scientific management, it is essential that all these are measured precisely and should not be based on mere estimates. This approach can be adopted in all aspects of management.
Harmony in Group Action
Taylor has emphasized that attempts should be made to obtain harmony in group action rather than discord. Group harmony suggests that there should be a mutual give and take on a situation and proper understanding so that group as a whole contributes to the maximum.
Cooperation
Scientific management involves achieving cooperation rather than chaotic individualism. Scientific management is based on mutual confidence, cooperation, and goodwill. Cooperation between management and workers can be developed through mutual understanding and a change in thinking.
Taylor has suggested the substitution of war for peace, hearty and brotherly cooperation for contentment and strife, replacement of suspicious watchfulness with mutual confidence, of becoming friends instead of enemies. It is along this line, I say, that scientific management must be developed.
Maximum Output
Scientific management involves continuous increases in production and productivity instead of restricted production either by management or by workers. Taylor hated inefficiency and deliberate curtailment of production. His concern was with the large size of the cake.
In his opinion, there is hardly any worse crime to my mind than that of deliberately restricting output. He decried quarrels over production but welcomed quarrels over distribution, provided the product to be distributed had outgrown the size.
Therefore, he advised the management and workers to turn their, attention towards increasing the size of the surplus until the size of the surplus becomes so large that it is necessary to quarrel over how it shall be divided.
Development of Workers
In scientific management, all workers should be developed to the fullest extent possible for their own and for the company‘s highest prosperity.
The development of workers requires their scientific selection and providing them training at the workplace. Training should be provided to workers to keep them fully fit according to the requirement of new methods of working which may be different from the non-scientific methods.
FAQs Section
What are the features of scientific management?
Separation of Planning and Doing, Functional Foremanship, Job Analysis, Standardization, Scientific Selection and Training of Workers, Financial Incentives, Economy, and Mental Revolution are the features of scientific management.
What are the principles of scientific management?
The principles of scientific management are:
1. Replacing the Rule of Thumb with Science
2. Harmony in Group Action
3. Cooperation
4. Maximum Output
5. Development of Workers.